Benefits of Automating Depalletizing Process
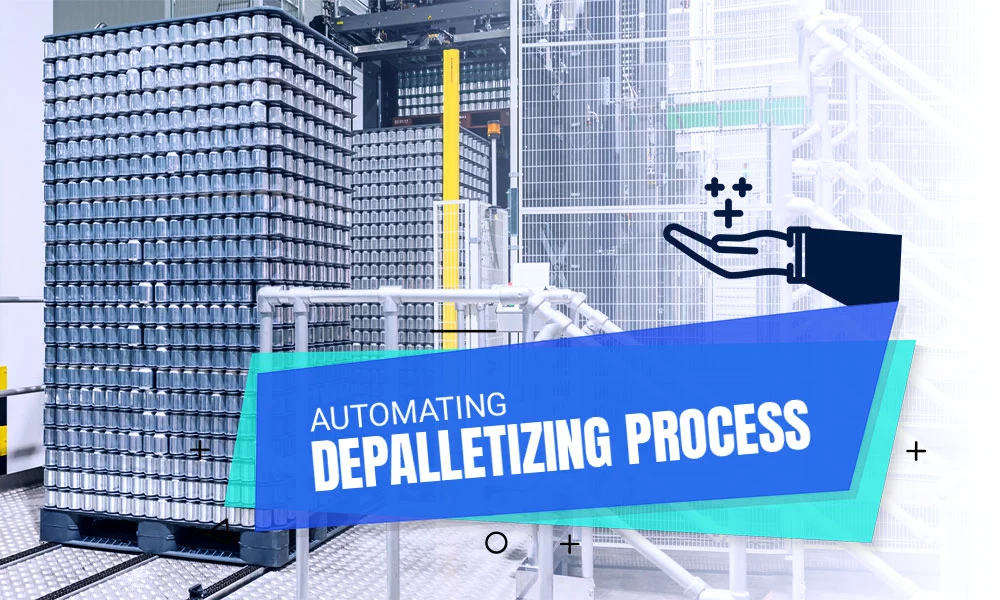
Depalletizing removes items from a shipping pallet, sometimes called singulation or decanting.
It traditionally entails strenuous, physically demanding actions, such as repeated heavy lifting, bending, and stretching. If the package weighs more than 25 kg, this physical exertion may be hazardous.
In the United States, the demand for warehouse labor has increased dramatically, especially during the pandemic. Social distancing and quarantine measures have also been yet another huge hurdle. Manual pickers are obliged to labor long hours and are constantly under pressure to lift goods of various sizes, shapes, and weights.
Due to all those factors, automating the depalletizing process seemed to be a reliable option.
Thanks to a robot control system with a built-in depalletizing function, it is possible to load and unload an object without spending a lot of time on training. Any project can benefit from the use of robotic work cells.
Many industries and businesses now use palletizing robot technology to automate their operations. The robotic depalletizing systems boost production and profits while allowing greater product flexibility and longer run times.
Limitations with Traditional Depalletizing Methods
Robotic technology was limited to selecting products with similar characteristics. As a result, the pre-programmed system could not handle SKU variations (Stock Keeping Unit).
There is no denying that people are endowed with the cognitive intelligence to locate the item, select it at their own time, and arrange it appropriately. Warehouse personnel must have job and safety training to function accurately.
Human workers at risk cost businesses injury claim charges, safety training, and legal compliance costs, contributing to a high turnover rate. Furthermore, companies must balance employing new employees with maintaining or improving throughput.
Likelihood of developing chronic bodily ailments According to a University of North Carolina survey, more than 36% of warehouse manual workers have back and shoulder injuries, resulting in missed workdays due to lifting and handling essential things.
Other prevalent issues with manual handling include physical limits, a lack of supervision, and poor ergonomics. Hence, there was a need to construct a dependable depalletization cell-free of human pickers.
Thanks to deep-learning algorithms, warehouses can now utilize a suitable robotic depalletizing cell with a cutting-edge vision system and an appropriate gripper to carry the heaviest of things.
Considerations for Automating the Depalletizing Process
Installing vital depalletizer cells in warehouses allows for more efficient use of the authorized area, including the floor and the vertical space. This can improve overall performance by allowing manual workers to focus on more value-added jobs.
A robotic depalletizer has 3D vision systems and a gripper for pick-and-place depalletizing operations. Multiple cameras, vision software, and laser sensors comprise 3D machine vision systems. A cutting-edge 3D vision system not only captures the environment but also determines the locations of randomly placed items. It enables robots to scan each object, identify their pick point, and put the thing on a conveyor belt. The advanced robotic depalletizer cell can recognize a box with tapes as a single item rather than six individual boxes.
Vision software for a robotic depalletizing cell smoothly integrates hardware and software components. Robots can pick heavy things from a random stack using vision software that improves object segmentation accuracy. An example of system integrators’ software is Fizyr’s vision software. It is capable of dealing with tightly stacked and overlapping boxes.
Using Visual Technologies to Automate Depalletization
With AI-driven vision technology and machine-learning algorithms, robots can quickly offload overlapping objects or shiny products.
A robotic depalletizer can manage a continuous flow of mixed-SKU pallets in any order using its powerful vision software. It can quickly recognize the item on the pallet, identify variants, and manage them appropriately.
The advanced vision software segments the item and classifies it. It suggests over a hundred grip poses depending on the trained neural network, allowing robots to move more quickly under challenging conditions. It eliminates typical manual handling errors while keeping a consistent throughput rate.
Automated robotic depalletizing, whether for mixed-SKU pallets or many pallets of the same SKU, increases productivity, lowers operating costs, and offers a safe workplace. On the other hand, warehouse workers are less prone to chronic diseases, accidents, and other medical problems. Most importantly, the business benefits from both artificial and human cognitive intelligence.